Tessa Sandstrom: Myths Vs. Facts About Bakken Crude And Oil By Rail
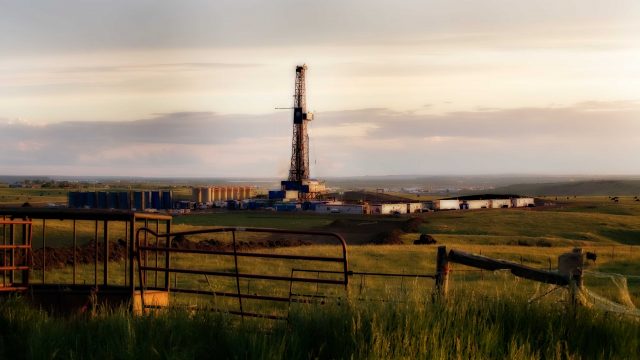
The transportation of crude oil by rail has been a top issue the last few months. In discussing this topic, one of the speculations was that Bakken crude may (please note: may) have been more volatile than other light sweet crudes, and therefore more dangerous to haul than many other hazardous materials that traverse the nation’s rails daily, including ethanol, gasoline, diesel or other types of crude oil. That speculation was recently disproven by three separate independent studies, but still the misconceptions about Bakken crude continue to spread.
Myth: Bakken crude is more volatile than other crude oils
FACT: Three independent studies have shown that Bakken crude is similar to other North American light, sweet crude oils in gravity, vapor pressure, flash point and initial boiling point. According to these studies, Bakken’s gravity, or density, is 41 degrees, which classifies it as a light sweet crude and is comparable to other light crudes, which are defined as having a gravity of 31.1 degrees or more.
Turner, Mason and Company, one of the contractors commissioned to study Bakken crude characteristics, found that the average vapor pressure for the commodity was between 11.5 and 11.8 pounds per square inch (PSI), which is virtually the same as other light crudes.
In fact, U.S. Senators Jeff Merkley and Ron Wyden have acknowledged this and have rightly shifted focus on ensuring all hazardous materials, including ethanol, gasoline, diesel and crude oils, are transported safely.
Myth: Bakken crude is corrosive and damages tank cars.
FACT: Corrosivity is defined by the U.S. Department of Transportation as having the ability to corrode a tank car by a half a centimeter per year. Sulfur weight and acidity, measured by the total acid number (TAN) are two contributors to corrosivity. Bakken crude’s sulfur weight of .14 percent classifies it as a sweet crude and well below the .5 percent threshold upon which it would be considered a sour crude. Comparatively, Bakken crude’s TAN is 0.1 to 0.2 milligrams of potassium hydroxide per gram (mg KOH/g) is low and comparable to West Texas Intermediate crude, a common benchmark crude. Crudes below 0.5 mg KOH/g is considered low TAN and rarely a concern. Crudes above 1.0 are considered high TAN, and require special refinery processing techniques.
Myth: Bakken crude contains gases that make it more hazardous
FACT: The vapor pressure is a measure of a liquid’s ability to hold gases rather than releasing them into vapor. The Bakken’s average vapor pressure is an indicator that the liquid portion continues to hold on to those gases despite seasonal temperatures. Questions arose as to whether or not Bakken crude had a tendency to release vapors during transit. The Turner, Mason and Company study measured vapor pressure at the loading site in North Dakota and was measured again at the point of delivery 1,700 miles away in Louisiana. Results showed that the vapor pressure remained unchanged, showing that Bakken crude remains consistent even during transit.
Myth: Current DOT-111 tank cars are insufficient to haul Bakken crude
FACT: DOT-111 tank cars are designed to accept vapor pressures of up to 100 PSI, which means even the Bakken’s maximum vapor pressure of 14.4 is three times lower than the accepted threshold. These same tank cars are used to haul ethanol, gasoline and diesel fuel, all of which also meet the criteria for these tank cars.
Myth: Bakken crude has been misclassified during shipping
FACT: Bakken crude has been properly classified as a Packing Group I or II flammable liquid based on its flash point and initial boiling point. The study conducted by Turner, Mason and Company did identify flaws in the classification methodology, however. The limitations of the test required for measuring initial boiling point can result in the same sample of crude being assigned to Packing Group I (<95°F IBP) or Packing Group II (>95°F IBP). The American Petroleum Institute is currently working to determine improved, more precise classification standards for assigning flammable liquid packing groups to ensure maximum consistency and safety in the transportation of crude oils. Packing Group I or II materials are still hauled in the same type of railcar and elicit the same emergency response in the case of an accident.
Myth: Bakken crude needs to be stabilized or have light ends stripped before transit
FACT: Data from the studies show that Bakken crude is not more volatile or flammable than other crudes. With a vapor pressure of 11.5-11.8 PSI, Bakken crude falls well below the safety margins built into railcars and well below the 43.5 PSI threshold between flammable liquids and flammable gases according to the DOT regulations.
Stripping of NGLs is used typically in the condensate window where API gravity is above 50 degrees. At API gravities of 50-60 degrees, stabilization is required for pipeline transportation and required by EPA environmental standards. Bakken crude has an average API gravity of 41, which falls below the EPA tank vapor guidelines, so it doesn’t make sense for industry or regulators to explore stripping the NGLs from Bakken. In most cases, “stabilization is used to fulfill market demand for light materials.” There is currently not a market demand for these lighter ends in North Dakota, however, and removing them from crude oil would require their transport by rail car to the Gulf Coast or East and West Coast where markets currently exist.
The NDPC welcomes the establishment of these markets, however, to contribute to a growing and diversified North Dakota economy.
Despite these and other perpetuating myths, sound scientific data consistently show that Bakken crude is a high quality commodity that is safe to haul by rail. Regulators and leaders such as Merkley and Wyden have recognized this and have shifted focus to the root of incidences involving Bakken crude: the derailments themselves.
Safety always has and continues to be a core value of the oil and gas industry and the goal is zero incidents. The NDPC and its members believe rail safety improvements must be developed using a holistic, comprehensive, and systematic approach that examines prevention, mitigation, and response. Safety solutions must be data-driven and produce measurable improvements to safety without creating new risks or inadvertently shifting the risks to other businesses or operations. To achieve this, collaboration is needed among government, shippers, railroads, and tank car builders.
The NDPC met with the White House Office of Management and Budget on July 7 to discuss these characteristics and find ways we can continue to work together to enhance safety in bringing this product to market and ensuring our state can continue to improve our energy security by providing a reliable energy resource for our nation.